Servo size, distance of operation and reliability of throw.
Servo size, distance of operation and reliability of throw.
IME from decades ago PECO solenoid motors were at limit of effective point operaton through a board af around 26mm (12mm ply, 12mm fbre board, 2mm cork). Although the solenoid worked the right distance the 1 or 2mm of flex in the needle meant it was at full extent of reliable use.
I've yet to use servos for my planned loft railway but 9g servos seem to be the default and I see 9g does mean 9 gram motor size.
What is the effective/reliable baseboard depth for these when mounted underside?
I've seen some bigger servos being used, such as in this video "Turnout control with servos"
https://www.youtube.com/watch?v=mQWWVmHUCv0
I see others asked why the bigger servos, but no answer. Anyone here find they need bigger or beefier than the 9g?
I also see some 9g servoson ebay mention "Metal gear". Is that better/worse for us in model railways?
They operate digitally going from defined range say 800 to 1100 in the demo I watched. Very precise.
If the servo is used 100 times won't it become out of synch and mean servos have to constantly be tweaked or do they have an inbuilt zero position that doesn't stray?
TIA
Dave
I've yet to use servos for my planned loft railway but 9g servos seem to be the default and I see 9g does mean 9 gram motor size.
What is the effective/reliable baseboard depth for these when mounted underside?
I've seen some bigger servos being used, such as in this video "Turnout control with servos"
https://www.youtube.com/watch?v=mQWWVmHUCv0
I see others asked why the bigger servos, but no answer. Anyone here find they need bigger or beefier than the 9g?
I also see some 9g servoson ebay mention "Metal gear". Is that better/worse for us in model railways?
They operate digitally going from defined range say 800 to 1100 in the demo I watched. Very precise.
If the servo is used 100 times won't it become out of synch and mean servos have to constantly be tweaked or do they have an inbuilt zero position that doesn't stray?
TIA
Dave
Re: Servo size, distance of operation and reliability of throw.
Hi
There are basically two types of Servo.. Digital and Analogue. IMO for point operation use Analogue and for other scenic operations such as semaphore signals and operating accessories like engine shed doors opening and closing or level crossing gates etc use the the Digital version.
As for baseboard depth and operating drive pin length my baseboards are 11mm thick and by using servo mounts (Produced by MERG in my case) they work very easily.
I had a Demonstration board with 9g servos fitted and that was 15mm thick Contiboard and the points worked perfectly (See picture below). I have removed the over centre spring on all my points, as that allows a nice slow movement of the point blades but the spring can be left if wished.
The main things IMO when using Servos are... Ensure the control circuits are feed from a regulated DC power supply capable of outputting at least 4.0Amps or more. Keep the three servo control wires as short as possible too.
The Servo control electronics hold the servo in whatever the required position is, so they will always be set correctly.
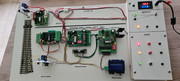
There are basically two types of Servo.. Digital and Analogue. IMO for point operation use Analogue and for other scenic operations such as semaphore signals and operating accessories like engine shed doors opening and closing or level crossing gates etc use the the Digital version.
As for baseboard depth and operating drive pin length my baseboards are 11mm thick and by using servo mounts (Produced by MERG in my case) they work very easily.
I had a Demonstration board with 9g servos fitted and that was 15mm thick Contiboard and the points worked perfectly (See picture below). I have removed the over centre spring on all my points, as that allows a nice slow movement of the point blades but the spring can be left if wished.
The main things IMO when using Servos are... Ensure the control circuits are feed from a regulated DC power supply capable of outputting at least 4.0Amps or more. Keep the three servo control wires as short as possible too.
The Servo control electronics hold the servo in whatever the required position is, so they will always be set correctly.
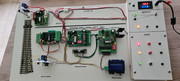
-
- Posts: 412
- Joined: Fri Oct 05, 2018 6:49 pm
- Contact:
Re: Servo size, distance of operation and reliability of throw.
In cases where strength and hard wearing is required metal gears are preferred in most applications not only in servos. Metal gears can be noisy and need lubrication although using sealed gearboxes usually does not require the user to add lubrication.
Nylon gears can be quieter and nylon does not require lubrication. In a 9g servo using metal gears is more about hype than anything else.
Richard
Re: Servo size, distance of operation and reliability of throw.
Brian. I'm surprised you say analogue. I should have mentioned I plan to use them via arduino boards, but you know that.
I'd assume analoge means they can be turned on or off but no control as extent of throw.
Do the analogue accept commands from arduino firmware?
Noted re circuits, I plan on having buzz/common cable feeding the arduino that then has multiblock connector to servo.
Therefore arduino boards will be located near point clusters, to minimise cable distance (for neatness) but take your inference on reducing resistance.
Shame you are over in Kent, I think we'd have much in common. The control board looks great, very neat, though the points should be on the opposite side
The last time I did this, was into a white painted ply control panel. Even on an average layout the number of wires/LED's made it hard to cram it all in.
Also, when layout is changed or added to, it isn't easy to change the panel.
I'm hoping the GUI route control panel will almost update itself just by entering minimal data.
Richard: I'll go for non metal then. These things always have pros/cons and realise r/c model likely have different needs. Not requiring lubrication is certainly a benefit to go for.
Thank-you to both. Dave
I'd assume analoge means they can be turned on or off but no control as extent of throw.
Do the analogue accept commands from arduino firmware?
Noted re circuits, I plan on having buzz/common cable feeding the arduino that then has multiblock connector to servo.
Therefore arduino boards will be located near point clusters, to minimise cable distance (for neatness) but take your inference on reducing resistance.
Shame you are over in Kent, I think we'd have much in common. The control board looks great, very neat, though the points should be on the opposite side

The last time I did this, was into a white painted ply control panel. Even on an average layout the number of wires/LED's made it hard to cram it all in.
Also, when layout is changed or added to, it isn't easy to change the panel.
I'm hoping the GUI route control panel will almost update itself just by entering minimal data.
Richard: I'll go for non metal then. These things always have pros/cons and realise r/c model likely have different needs. Not requiring lubrication is certainly a benefit to go for.
Thank-you to both. Dave
- teedoubleudee
- Posts: 1116
- Joined: Fri Oct 05, 2018 2:53 pm
- Location: Downham Market
- Contact:
Re: Servo size, distance of operation and reliability of throw.
Hi Dave, I use servos for all my point motors, those ubiquitous blue plastic Tower 9 gram ones, cheap as chips. Depending on the driver electronics they can be distanced away - I have used servo extension cables of two meters without issue. It's important to remove the point springs to remove any resistance and give a nice smooth quiet transition.
Most people are shocked when they find out how bad I am as an electrician
Re: Servo size, distance of operation and reliability of throw.
Analogue Servos can be adjusted for the amount of throw both ways and their speed of movement. This is all done by the Servo control board.
I use MERG CBUS control for all accessories and DCC for loco control. CBUS uses a twisted pair for data and a 12v + and - supply for everything else. Sorry, I haven't used Arduino other than in the MERG EzyBus system, which currently I haven't used beyond experimenting with them. But I do have a load of EzyBus Mk1 input and Output modules. The Output module uses Nano Arduino, though later versions have done away with the Arduino and use ATMEGA328P chips on the PCBs.
I use MERG CBUS control for all accessories and DCC for loco control. CBUS uses a twisted pair for data and a 12v + and - supply for everything else. Sorry, I haven't used Arduino other than in the MERG EzyBus system, which currently I haven't used beyond experimenting with them. But I do have a load of EzyBus Mk1 input and Output modules. The Output module uses Nano Arduino, though later versions have done away with the Arduino and use ATMEGA328P chips on the PCBs.
- teedoubleudee
- Posts: 1116
- Joined: Fri Oct 05, 2018 2:53 pm
- Location: Downham Market
- Contact:
Re: Servo size, distance of operation and reliability of throw.
I use the MegaPoints servo controllers. I did try coding my own controller but got intermittent twitching issues. I find the Megapoints system ultra reliable.
Most people are shocked when they find out how bad I am as an electrician
Re: Servo size, distance of operation and reliability of throw.
TDD. That sounds good. On Megapoints system home page has Peter Waterman visiting Chester Cathedral.
I grew up in Chester so was enthused to see it on Hornby series on TV.
I've marked it to read and digest.
Brian: Also marked the 2 systems to read up.
I have to ask the obvious question.
If both analog and digital accept commands for precise control from PCB's etc then what makes one analog and the other digital?
You know the answer Brian but for me and readers this explains it:
https://www.radiocontrolinfo.com/the-di ... rc-servos/
I note for analog it says "Weak Holding Torque".
If a train is routed to say turn left and then looped around for a while, bearing mind spring removal (as per TDD's coment) then would point come out of position - or is point servo automatcally re-activated for same direction on subsequent passes with no route change?
Your digital/analogue reference has stopped me buying the wrong thing. So subtle a thing yet would have been a shocker to realise post instalation, thank-you for taking the trouble to explain.
I grew up in Chester so was enthused to see it on Hornby series on TV.
I've marked it to read and digest.
Brian: Also marked the 2 systems to read up.
I have to ask the obvious question.
If both analog and digital accept commands for precise control from PCB's etc then what makes one analog and the other digital?
You know the answer Brian but for me and readers this explains it:
https://www.radiocontrolinfo.com/the-di ... rc-servos/
I note for analog it says "Weak Holding Torque".
If a train is routed to say turn left and then looped around for a while, bearing mind spring removal (as per TDD's coment) then would point come out of position - or is point servo automatcally re-activated for same direction on subsequent passes with no route change?
Your digital/analogue reference has stopped me buying the wrong thing. So subtle a thing yet would have been a shocker to realise post instalation, thank-you for taking the trouble to explain.

Re: Servo size, distance of operation and reliability of throw.
MegaPoints used to twitch as well but that got resolved in an update ages ago. I use them also. Great kit. R-teedoubleudee wrote: ↑Sun Jan 16, 2022 7:01 pm I use the MegaPoints servo controllers. I did try coding my own controller but got intermittent twitching issues. I find the Megapoints system ultra reliable.
Young at heart. Slightly older in other parts.
- teedoubleudee
- Posts: 1116
- Joined: Fri Oct 05, 2018 2:53 pm
- Location: Downham Market
- Contact:
Re: Servo size, distance of operation and reliability of throw.
Dave, regarding your query ref points losing their position. If you use a springy activation wire (Megapoints sell ideal wire for this) and set the servo limits so there is light pressure holding the point blades (and I do mean light - test by pushing against it) then the point will hold it's position. Don't overdo this setting as it could harm the servo,
Most people are shocked when they find out how bad I am as an electrician
Who is online
Users browsing this forum: No registered users and 7 guests